eye on equipment
Back Room Solutions
Karlen McLean, ABOC, NCLC
From installation to initiation, in-office labs can raise profits and, along the way, questions. Addressing issues before they become problems helps keep labs running smoothly.
Here are some up-front questions about “in the back” answered by equipment experts.
Q If I invest in new edging equipment, what details should I look for? I'm particularly interested in the ability to add on features in the future.
A Think of how you see your business today and also in the next one to three years.
Do you foresee more high-end specialty design-centric jobs? Or more traditional metal/zyl jobs that don't need exceptional technology?
Edging systems now exist that can cater to any specific ECP in-office business model, be it standardized edging, beveling, polishing, wrap, special design edge cuts, jewel inlays, and 3D drilling and grooving.
The type of work you expect to do dictates the initial investment model. Some models offer a “sidecar” drilling unit which can be added on after the edger purchase, once you're ready to take on drilling work or after the edger has paid for itself through lab savings.
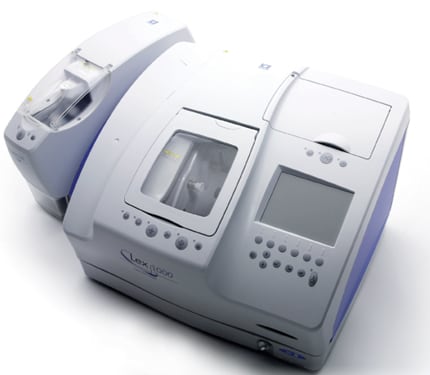
New equipment should meet your office needs for the next three years. Image courtesy of Santinelli International
Other new models offer software upgrades that give you the ability to expand into more sophisticated types of jobs, such as faceting, partial groove, and design cut features.
For example, we offer software that can be added to our model ME-1000 to create customized magnetic sunlenses.
— Steve Swalgen, national director, lab business, Santinelli International
Q Our in-house finishing lab never really met expectations. How can we start to revive it?
A Ask yourself a few questions to explore why the lab hasn't met expectations.
People Protocol Q With a start-up in-office lab, what personnel do you recommend? Then, what steps should I take to properly staff the lab as it gets busier? A The type of equipment you choose will have an effect on the number of employees needed. Research equipment manufacturers, as they can provide valuable insight. They've seen successes and potential roadblocks, and they can help determine the equipment and number of employees you'll require. They can also put you in touch with an ECP who has an in-office operation. A phone call or visit with them can help you have a better understanding of the preparation and personnel you'll need. While it's best to hire a lab employee with experience, only minimal optical skills are needed for finishing. When considering in-office surfacing, it's recommended that you invest in at least one employee with an optical background. Place an ad in your local newspaper or in industry trade journals. With the continual consolidation of larger labs, finding experienced employees may be easier than you think. — Kevin Paddy, director of business development, National Optronics |
■ QUESTION: Was the staff properly trained to use the edger to its full capacity?
ANSWER: Train and retrain your in-house lab staff.
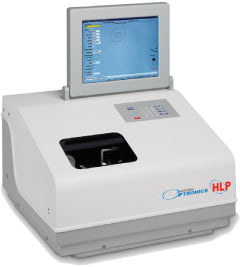
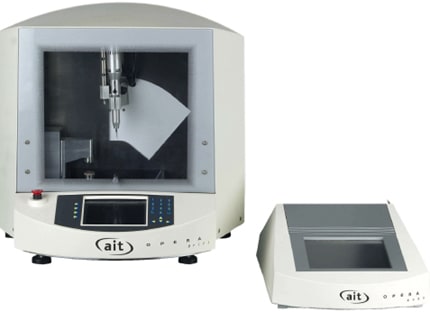
For the best performance, ensure that your staff is trained and equipment maintained. Image above: AIT, and below: National Optronics
■ QUESTION: Was the staff effectively motivated to make the lab work?
ANSWER: Examine your staff compensation policy.
■ QUESTION: Did the owner set adequate expectations for the staff?
ANSWER: Set specific goals.
■ QUESTION: Did the edger that was purchased meet the requirements for the practice?
ANSWER: If not, is an upgrade possible? Work with your equipment provider.
■ QUESTION: Has the edger been properly maintained and serviced?
ANSWER: Run the routine maintenance functions as directed by your owner's manual.
Occasionally when an edger is purchased, the staff hasn't been included in the decision and is not entirely happy about edging. They see it as more work on their part with no additional compensation. With proper training, usually the staff comes around to in-office edging when they realize that knowing how to operate an edger gives them job security in the practice, especially in this tough economic climate.
Additionally, staff may not use the edger to full capacity, and work that can be done in-office is still being sent to an outside lab. Retraining can help solve this.
The biggest reason in-office edging may not be completely successful is because there's not someone in charge to make sure it happens.
When you add edging, your way of doing business changes, and perhaps not everyone is open to those changes.
It's easy to end up going back to business as usual.
— John Hemphill, national sales manager, Briot USA EB